Overview
- The Isotopx DG60 is a floor standing, self contained filament degassing unit capable of automatically preparing up to 60 TIMS filaments per cycle.
- The most advanced software control of any commercially available TIMS degasser.
- Filaments split into banks of 10, each with its own degassing method consisting of multiple ramp and hold steps. No other TIMS degasser offers this versatility.
- ‘No compromise’ oil-free vacuum system ensures rapid pumpdown and a clean degassing environment.
- Suitable for Isotopx Phoenix, Isoprobe-T and VG Sector 54 filaments. Please ask about filaments for other TIMS systems.

60 Filament Capacity
- Capable of degassing 10, 20, 30, 40, 50 or 60 filaments per run.
- Degassing is performed sequentially in batches of 10 or 20 filaments. This reduces the total power and cooling requirements and allows the DG60 to operate from a standard mains power outlet and use air cooling.
- For example, a method has a controlled ramp to 4A over 25 minutes followed by a 5 minute hold. Time per 10 or 20 filament batch is 30 min, total time for three batches (up to 60 filaments) approx. 90 mins. (plus pumpdown).
- Filaments not currently being degassed can optionally be heated to a low level to eliminate absorption of degassed material from hot filaments. Additionally a negatively charged baffle is inserted between filament banks to act as a vapour sink.
- Tools-free filament loading and unloading.
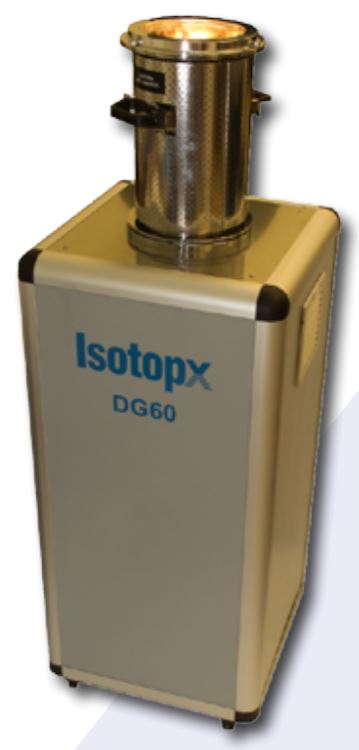
High Specification Vacuum System
- Stainless steel vacuum enclosure with sight glass.
- Oil-free vacuum pumping consisting of an air-cooled Pfeiffer Hi-Pace 300 L/sec turbo pump backed by Pfeiffer diaphragm pump.
- Ultimate vacuum 10-8 mbar.
- Pfeiffer dual-head (Pirani + cold cathode) vacuum gauge, capable of accurately measuring from atmospheric pressure down to 10-8 mbar.
- Vacuum constantly monitored within degas methods – filament current automatically reduced if the vacuum degrades significantly during degassing. The current is turned back up once the vacuum improves.
No tools Required
10 filaments are slotted into DG60 loading racks using a simple push-fit mechanism with filaments being firmly held in place by hidden spring contacts. The screws shown in the photograph (right) hold the spring clips in place and only need to be adjusted during degasser maintenance. Once loaded with filaments the racks are attached to the DG60.
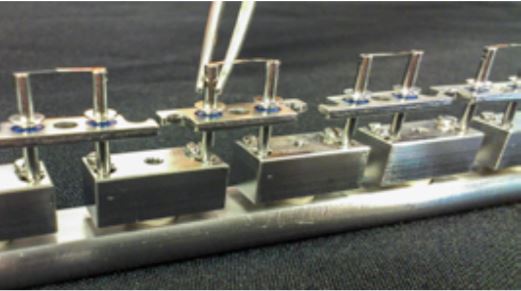
Using a single-handed ‘slot and turn‘ action as shown in photographs 1, 2 and 3 (left). DG60 holds up to six racks and from one to six racks can be loaded per run giving a capacity of 10 to 60 filaments in batches of 10. Each rack being used must be fully populated with 10 filaments for electrical continuity.
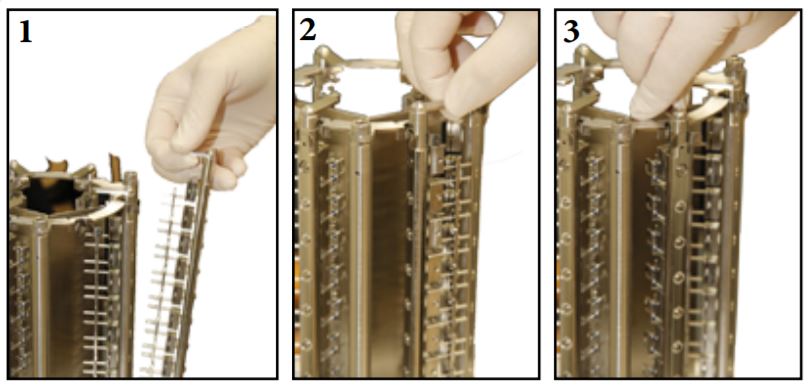
Sight glass
The top of the vacuum housing is transparent allowing filaments to be monitored during degassing. The photograph shows the ‘Y’ shaped metal baffle plate which is negatively charged to attract material degassed from filaments. The baffle separates the filament racks into pairs which will usually be degassed together.
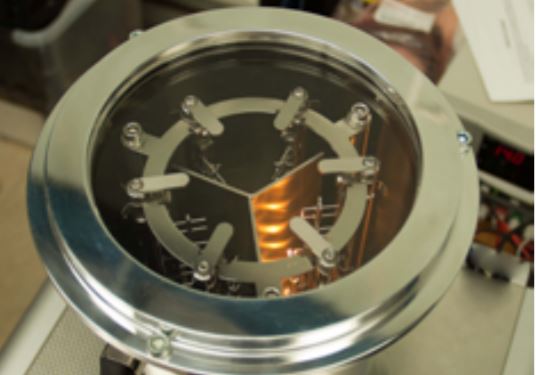
Advanced Software Control
DG60 has the most advanced software control of any commercially available degas bench permitting an unparalleled degree of automation. Each bank of 10 filaments can be programmed with its own degassing method allowing DG60 to prepare multiple filament types within a single degassing cycle. Each degassing method includes user-defined ‘ramp-to’ and ‘hold for’ steps. Multiple steps can be used in a single method allowing for a high level of customization. The DG60 user Interface provides feedback on system status and easy access to pump and vent controls. The control screen provides visualisations of filament current and vacuum over the course of the run. Manual control is available at any point allowing users to change the filament current in any one of the six banks within safety limits.
Set-up Wizard
The control software makes extensive use of set-up wizards guiding the user through the entire process.
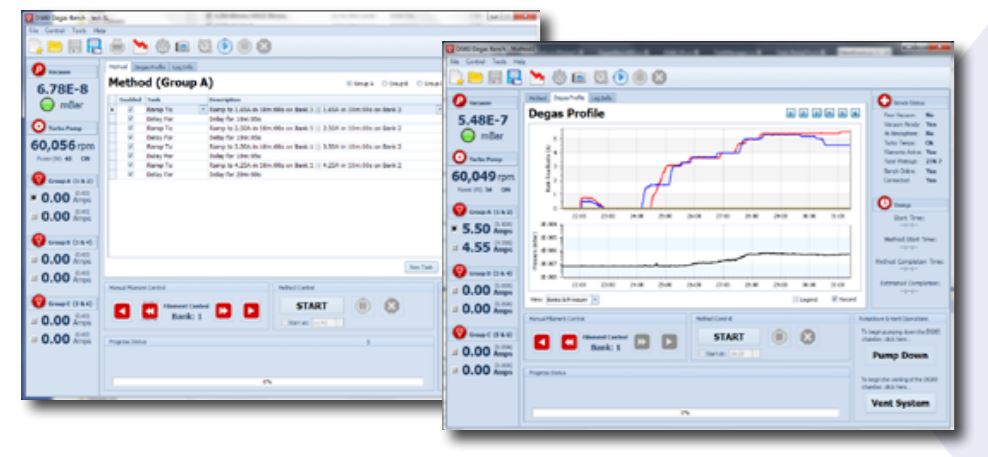
Pumpdown Wizard 1
The user chooses which of the six banks of filaments are to be degassed (10 filaments per bank). The banks are paired into three groups indicating the segregation provided by the metal baffle.
Each group uses its own degas program allowing for multiple filament types to be degassed in a single pumpdown cycle.
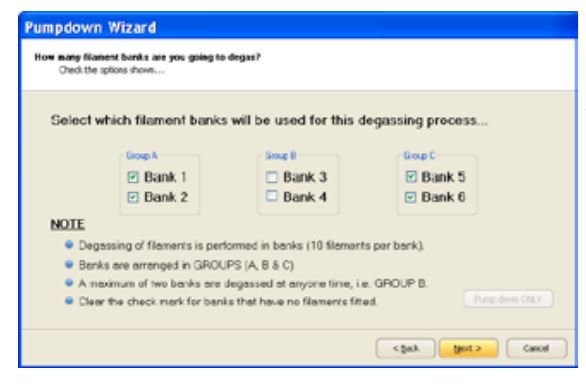
Pumpdown Wizard 2
The system performs an electrical continuity check to ensure that filaments are correctly positioned and there are no open-circuits or poor electrical contacts/joints.
This crucial step means that all electrical connections are checked before pumpdown.
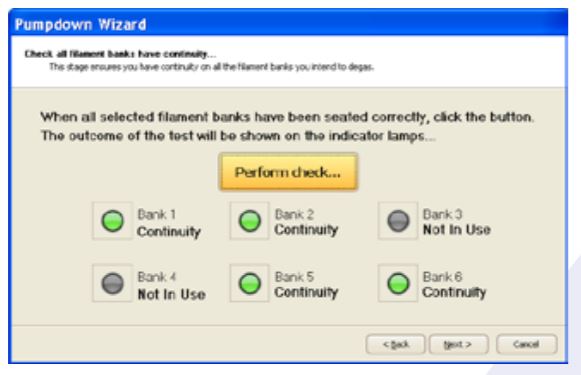
Pumpdown Wizard 3
Once electrical continuity has been confirmed the pumpdown cycle can be started. DG60 monitors pumpdown speed against the expected performance allowing it to identify leaks within the first 30 seconds after pumping has commenced. The operator is immediately notified if an error occurs and can rectify the problem.
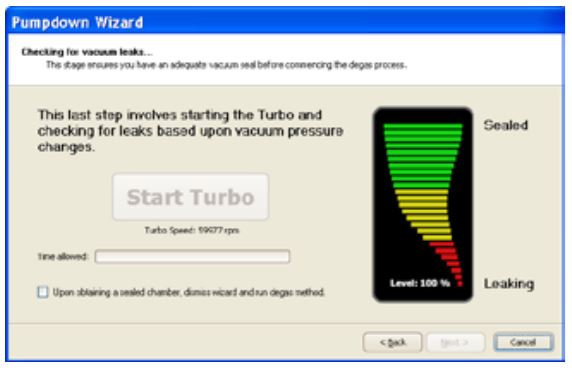
Download Product Information
Download the complete Product Information: DG60 Product Information